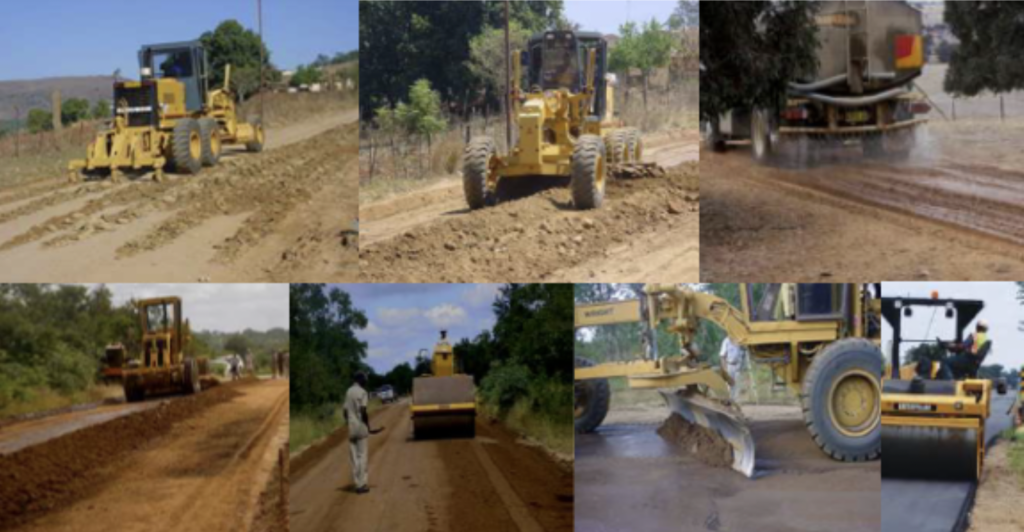
SoilBond® is an eco-safe, biodegradable, liquid copolymer used to stabilize and solidify any soil or aggregate as well as erosion control and dust suppression. Once applied to the soil or aggregate, the copolymer molecules coalesce forming bonds between the soil or aggregate particles. The key advantage of SoilBond® originates with its long molecular structure that link and cross-link together. As the water dissipates from the soil or aggregate, a durable and water-resistant matrix of flexible solid mass is created. Once cured, SoilBond® becomes completely transparent, leaving the natural landscape to appear untouched. For heavy road usage, top coating with asphalt will improve water resistance and hence prolong the service life of the road.
SoilBond® results are based on the application rate used. Modest application rates are useful for dust suppression and erosion control by creating a three-dimensional cap or surface crust. Heavier rates can generate qualities useful for soil solidification and stabilization found in road building.
Access roads or field working/storage areas can now be constructed with in-situ materials, reducing both cost and time of construction. SoilBond® also enables easier and cheaper maintenance once the road is constructed.
Application Notes
Application coverage and dilution rates may vary depending on traffic volume, load bearing capacity, soil type, weather conditions, soil moisture levels and compaction. All Mixed-in/Processed applications require laboratory and on-site testing to determine optimal application and dilution rates. Dilution rates for mix-in/processed applications are based on the difference between optimum moisture and in-situ moisture levels. There are different types of SoilBond® products designed to suit different types of native road materials and conditions. In general the application follow these steps:
- Site Preparation
- Soil Conditions – must be dry enough at least below optimum moisture level; at least enough to achieve optimum moisture level by application of 1 : 1 dilution of SoilBond
- Weather – The site must be free from rain at least 48 hours after SoilBond application
- Scarification – Scarify or till the soil completely (without clods) to the recommended depth
- Large Aggregates – Remove any large aggregate (10cm+) that could affect the final compaction
- Spray Equipment Preparation
- Spray Nozzles – Set spray nozzles to the desired width, height and output rate. Test equipment (off-site) if necessary.
- Coverage – The spray nozzles should provide an even coat over the treatment area with each pass.
- Spray Rate – Set the spray rate high enough to allow even coverage with multiple coats and low enough to prevent material from draining away from the treatment area.
- SoilBond Solution Preparation
- Water – Fill the application equipment (water truck) with the recommended volume of water.
- Dilution Determination: The total amount of water required to achieve optimum moisture must be field determined by comparing the in-place moisture content to the optimum moisture content (determined by a laboratory proctor test ASTM D2216-92). Testing the native soil for optimum moisture levels is required to determine the exact parts of water to use for diluting SoilBond® properly. Not enough water will generate dry spots / too much water will create mud or “pumping. Optimum moisture is critical when compacting for maximum compressive strength.
- SoilBond Addition – Fill the application equipment with the recommended volume of SoilBond® concentrate (see STANDARD COVERAGE RATES).
- Foaming: To prevent foaming, add the SoilBond® concentrate last, directly into the water.
- SoilBond Application
- Application – Apply the SoilBond solution evenly over scarified area
- Processing – Till, disc or manipulate the treated soil until the dilution is uniformly distributed into the soil.
- Grading – Contour, shape and crown the site to provide for proper drainage.
- Compaction – Compact the site to a minimum of 95% (per ASTM D 698 D 1557 modified Proctor Density). Optimally, use a pneumatic compactor for initial compaction to prevent soil adhering to the drum and finishing with a vibratory smooth steel drum compactor.
- Cleaning and Finishing
- Rinse – Rinse off all application equipment thoroughly with water until clean. If SoilBond® is allowed to dry and cure use a hot pressure washer or steam cleaner and brush to remove residue.
- Traffic – Prevent any human activity over the treated area until the site has completely cured.
- Curing – Allow the treated area to dry and cure for approximately 24 hours (@70°F/21°C).
- Topical Wear Coarse: If the mix-in/processed area is not going be covered with an alternate topical wear coarse (example: asphalt, concrete, chip-seal, etc.), then a topical application of SoilBond® must be applied as a topical road sealer and surface wear coarse (see “Standard Coverage Rates” for sealer).
Standard Coverage Rates
Application | Depth, cm | Coverage | |
M2/L | L/M2 | ||
Base Stabilization – Light | 10 | 1.1 | 0.91 |
Base Stabilization – Medium | 10 | 0.9 | 1.16 |
Base Stabilization – Heavy | 10 | 0.6 | 1.63 |
Base Stabilization – Light | 15 | 0.9 | 1.16 |
Base Stabilization – Medium | 15 | 0.6 | 1.63 |
Base Stabilization – Heavy | 15 | 0.4 | 2.72 |
Sealer over SoilBond base | 2.5 | 0.41 |